Welcome to our comprehensive guide on the "9 Best Practices in Reverse Logistics." In the fast-paced world of IT asset management, organizations face many challenges in efficiently handling product returns, optimizing inventory, and ensuring compliance with regulations. Whether you're a CIO, IT director, or asset manager, navigating these complexities effectively is crucial.
At UCS Logistics, we understand IT asset management's unique needs and challenges. This article delves into nine best practices to transform your IT asset management processes. From returns management to data analytics, supplier collaboration to recycling and disposal, these practices are the key to streamlining your operations, reducing costs, and enhancing sustainability.
Join us as we explore these practices in detail and discover how UCS Logistics can be your trusted partner on the journey to better IT asset management.
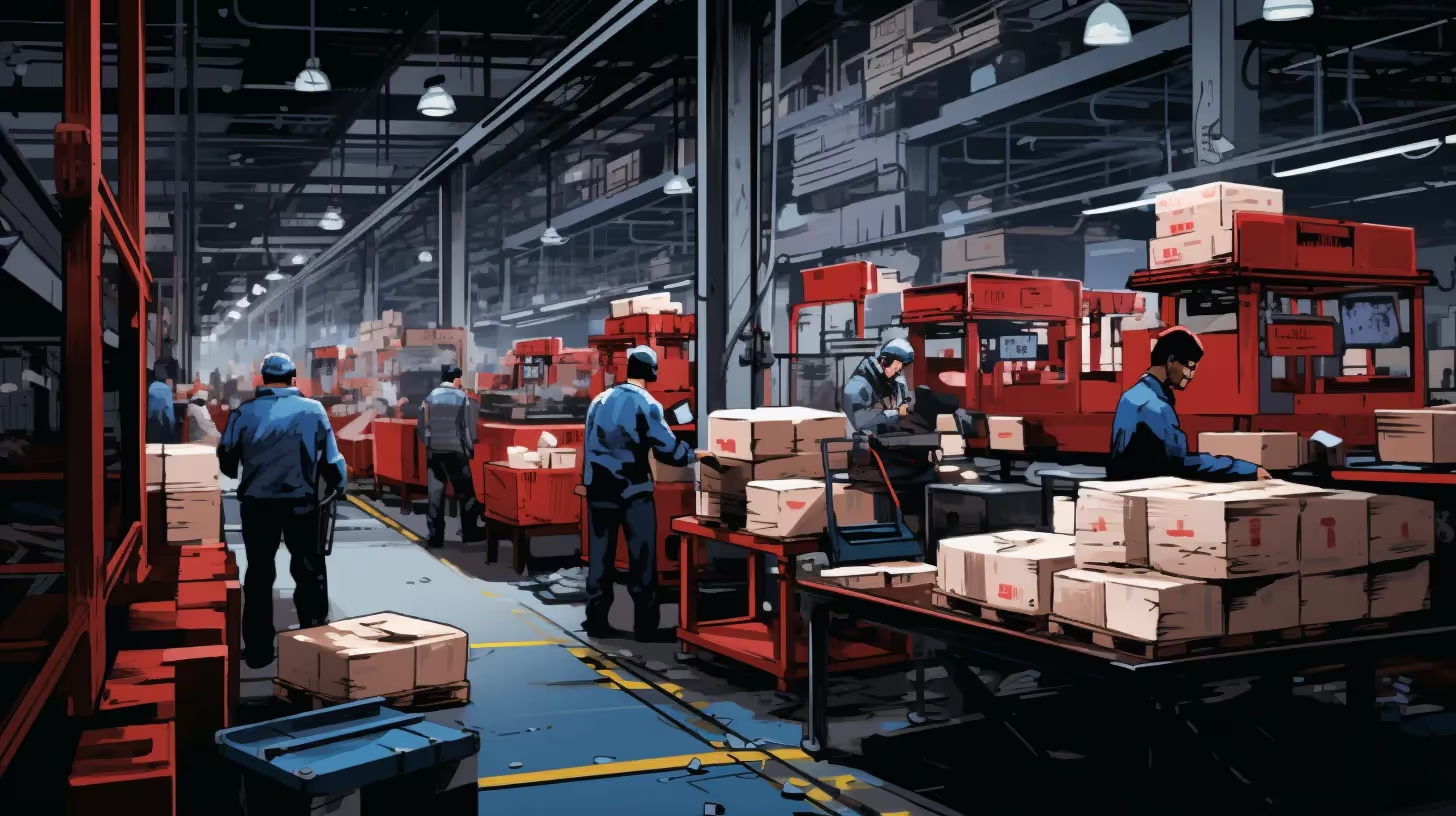
What Is Reverse Logistics?
Reverse logistics is a crucial aspect of supply chain management that deals with moving products and materials from their final destination back to the manufacturer or another designated location. It involves returning, remanufacturing, refurbishing, recycling, and disposing of products and materials.
Understanding the Importance of Reverse Logistics
Reverse logistics is pivotal in optimizing resource utilization and sustainability in various industries. It encompasses a range of activities aimed at reducing waste, recovering value from returned or used products, and minimizing the environmental impact of disposal.
Effective Returns Management
Effective returns management is a critical component of reverse logistics that focuses on efficiently handling product returns to minimize costs and maximize customer satisfaction. It involves several key processes and considerations:
Return Authorization
When a customer wishes to return a product, the first step is to initiate the return authorization process. This involves gathering information about the return, including the reason for the return, product details, and purchase history.
Inspection and Evaluation
Upon receiving the returned product, inspecting and evaluating its condition is essential. This step helps determine whether the product is eligible for resale, refurbishment, or needs to be disposed of.
Restocking
For products that are in good condition and suitable for resale, the next step is restocking. This involves returning the product to inventory for future sale to customers.
Refurbishment and Repair
In cases where returned products require refurbishment or repair, it is essential to have processes in place to address these needs promptly. Refurbished products can often be resold at a lower cost, benefiting both the company and customers.
Customer Communication
Clear and effective communication with customers throughout the returns process is crucial. Providing customers with updates on the status of their returns and refunds helps build trust and enhances the overall customer experience.
Inventory Management
Managing returned products in inventory efficiently is essential to avoid overstocking or understocking spare parts or refurbished items. An organized approach to inventory management ensures that returned items are readily available when needed.
Data Analytics
Data analytics tools can provide valuable insights into return trends, reasons for returns, and areas for process improvement. Companies can make informed decisions to optimize their returns management processes by analyzing data.
Please visit our website for more information on how UCS Logistics can assist with effective returns management and comprehensive IT asset management solutions.
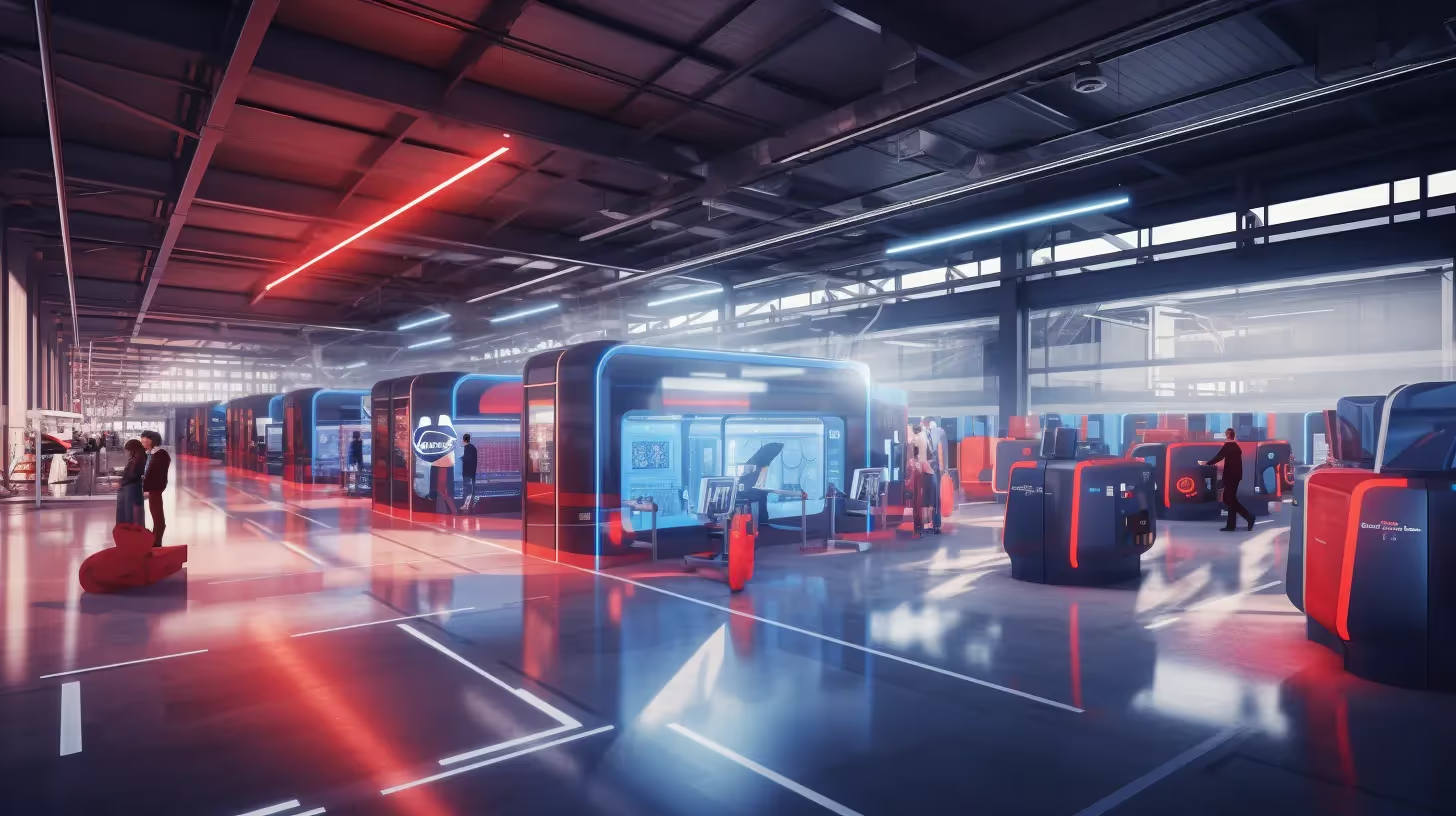
Product Evaluation and Sorting
In reverse logistics, product evaluation and sorting are essential processes that follow the initial return of products. These processes help determine the fate of returned items and play a crucial role in optimizing resource utilization and sustainability:
Evaluation of Product Condition
Upon receiving a returned product, the first step is to evaluate its condition thoroughly. This evaluation includes assessing whether the product is in a state suitable for resale, refurbishment, or recycling. Products may vary widely in condition, from like-new to heavily damaged.
Sorting for Resale
Products in good condition and can be returned to the inventory for resale are sorted accordingly. These items can be made available to customers again, reducing waste and maximizing revenue.
Refurbishment and Repair
Refurbishment and repair processes are initiated for products that require attention due to damage or wear and tear. Skilled technicians work to bring these items back to a sellable or usable state, extending their lifecycle and reducing the need for new replacements.
Recycling
Products that cannot be refurbished or resold due to extensive damage or obsolescence are sorted for recycling. Recycling ensures that materials are recovered and reused, contributing to sustainability efforts and reducing environmental impact.
Disposal
In cases where products are beyond repair and recycling, responsible disposal is critical. This involves adhering to environmental regulations and disposing of items in an eco-friendly manner to minimize environmental harm.
Inventory Management
Managing returned products in inventory efficiently is essential to ensure that they are readily available for resale or refurbishment. Effective inventory management prevents overstocking and understocking of spare parts or refurbished items.
Data Analytics
Data analytics tools play a vital role in product evaluation and sorting. By analyzing data on returned products, companies can identify trends, patterns, and opportunities for process improvement. Data-driven decisions can lead to more efficient sorting and resource allocation.
Inventory Management
Inventory management is crucial to reverse logistics and overall supply chain management. It involves handling returned products efficiently and ensuring they are accounted for in the inventory. Here are key aspects of inventory management in the context of reverse logistics:
Organized Tracking
Efficient inventory management starts with organized tracking of returned products. Each returned item should be documented accurately, including details about its condition, reason for return, and expected disposition.
Avoiding Overstocking
Proper inventory management helps companies avoid overstocking returned products. This prevents the unnecessary storage of excess items that may become obsolete and incur storage costs.
Preventing Understocking
Conversely, effective inventory management ensures enough refurbished or repaired items in stock to meet demand promptly. This ensures the timely delivery of customer orders.
Prioritizing Resale
Returned products that are suitable for resale should be prioritized within the inventory. This allows companies to recapture value from these items by making them available for purchase by customers.
Timely Handling
Inventory management also involves ensuring that returned items are handled promptly. Delays in processing returns can lead to increased storage costs and customer dissatisfaction.
Data Analytics
Data analytics tools play a vital role in inventory management. By analyzing data related to returned products, companies can make informed decisions about stock levels, trends, and areas for improvement.
Integration with Other Systems
Inventory management in reverse logistics should be seamlessly integrated with other systems, including order management and fulfillment, to ensure smooth operations.
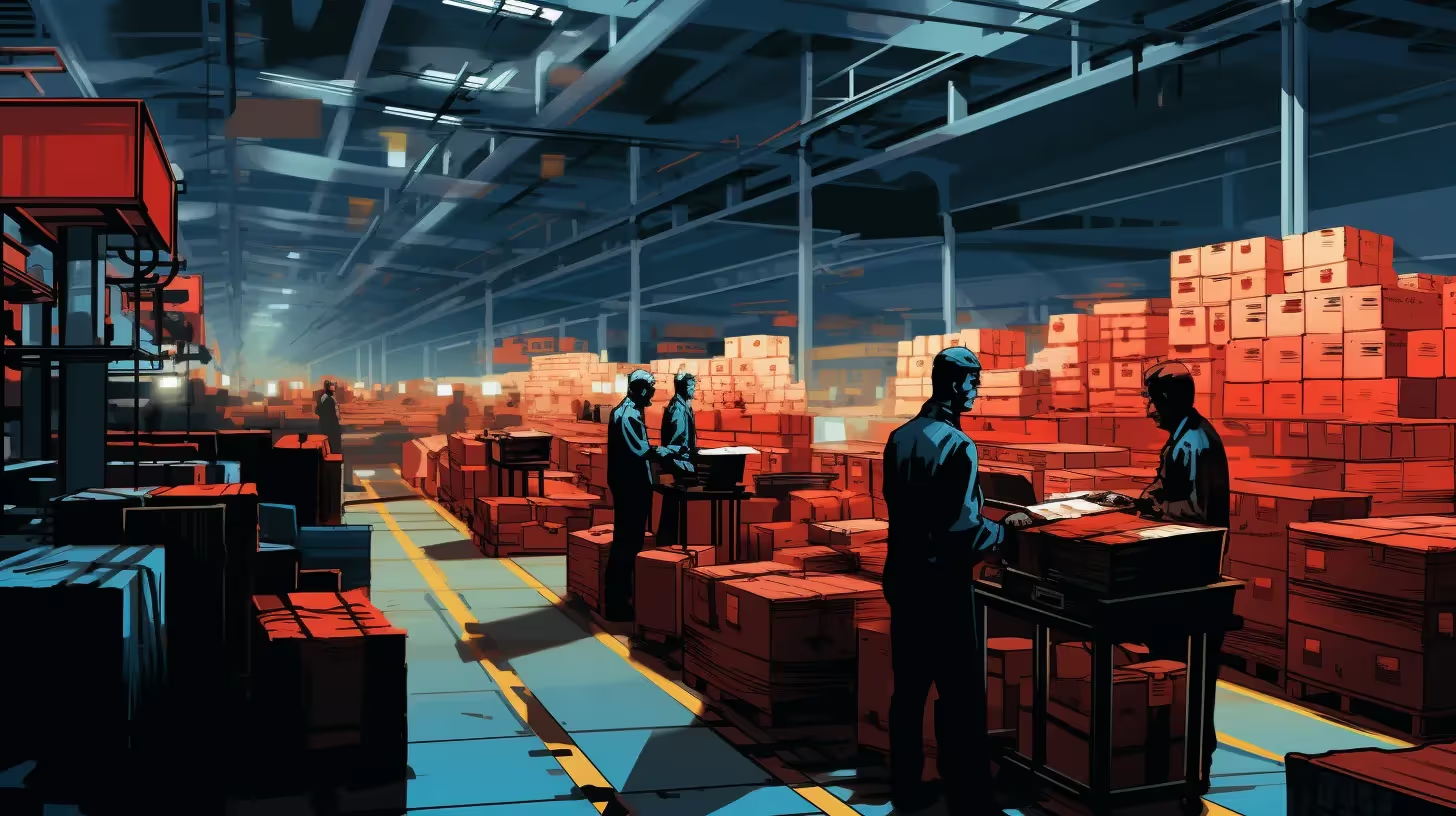
Data Analytics
Data analytics is crucial to effective reverse logistics and IT asset management. It involves the analysis of data related to returned products and various aspects of the supply chain. Here's a breakdown of the importance of data analytics in this context:
Insights into Return Trends
Data analytics allows companies to gain insights into return trends. By analyzing patterns, such as the types of products commonly returned or the reasons for returns, businesses can make informed decisions to address recurring issues.
Process Improvement
Analyzing data from reverse logistics processes helps identify areas for improvement. Based on data-driven insights, companies can streamline operations, reduce bottlenecks, and enhance efficiency.
Inventory Optimization
Data analytics aids in optimizing inventory levels. By studying inventory data, companies can adjust stock levels to meet demand effectively while minimizing carrying costs.
Customer Behavior Analysis
Understanding customer behavior is vital. Data analytics can reveal customer returns and preferences patterns, enabling companies to tailor their product offerings and services.
Forecasting
Data analytics can be used for demand forecasting. Predictive analytics helps businesses anticipate future returns and plan accordingly, reducing the risk of overstocking or understocking.
Integration with Other Systems
Data analytics should be integrated with other systems, such as inventory management and order fulfillment, to ensure a seamless flow of information and decision-making.
Supplier Collaboration
Supplier collaboration is key in optimizing reverse logistics and IT asset management. It involves working closely with suppliers to improve various aspects of the supply chain. Here are the primary reasons why supplier collaboration is crucial:
Streamlining Returns
Collaboration with suppliers is essential for streamlining the returns process. Suppliers need to be involved in return authorization, providing return labels, and coordinating the return of products.
Defective Products
When products are returned due to defects, working with suppliers to identify root causes and implement corrective actions is vital. This helps reduce the recurrence of defective products in the future.
Excess Inventory
Collaboration with suppliers can help address issues related to excess inventory. Suppliers may agree to take back excess products or provide flexible return policies to manage overstocked items.
Timely Replacement
Supplier collaboration ensures that replacement products are delivered promptly, minimizing customer downtime when replacements are needed for returned items.
Cost Reduction
Collaborating with suppliers can lead to cost reductions in the reverse logistics process. Shared responsibilities and efficient communication can reduce operational costs.
Quality Control
Collaboration with suppliers includes quality control measures. Suppliers and manufacturers can work together to improve product quality and reduce the number of returns.
Sustainability
Suppliers can play a role in environmentally responsible disposal and recycling of products. Collaborative efforts can ensure that end-of-life products are handled in an eco-friendly manner.
Continuous Improvement
Supplier collaboration should be an ongoing process. Regular meetings and feedback mechanisms enable continuous reverse logistics and supply chain management improvement.
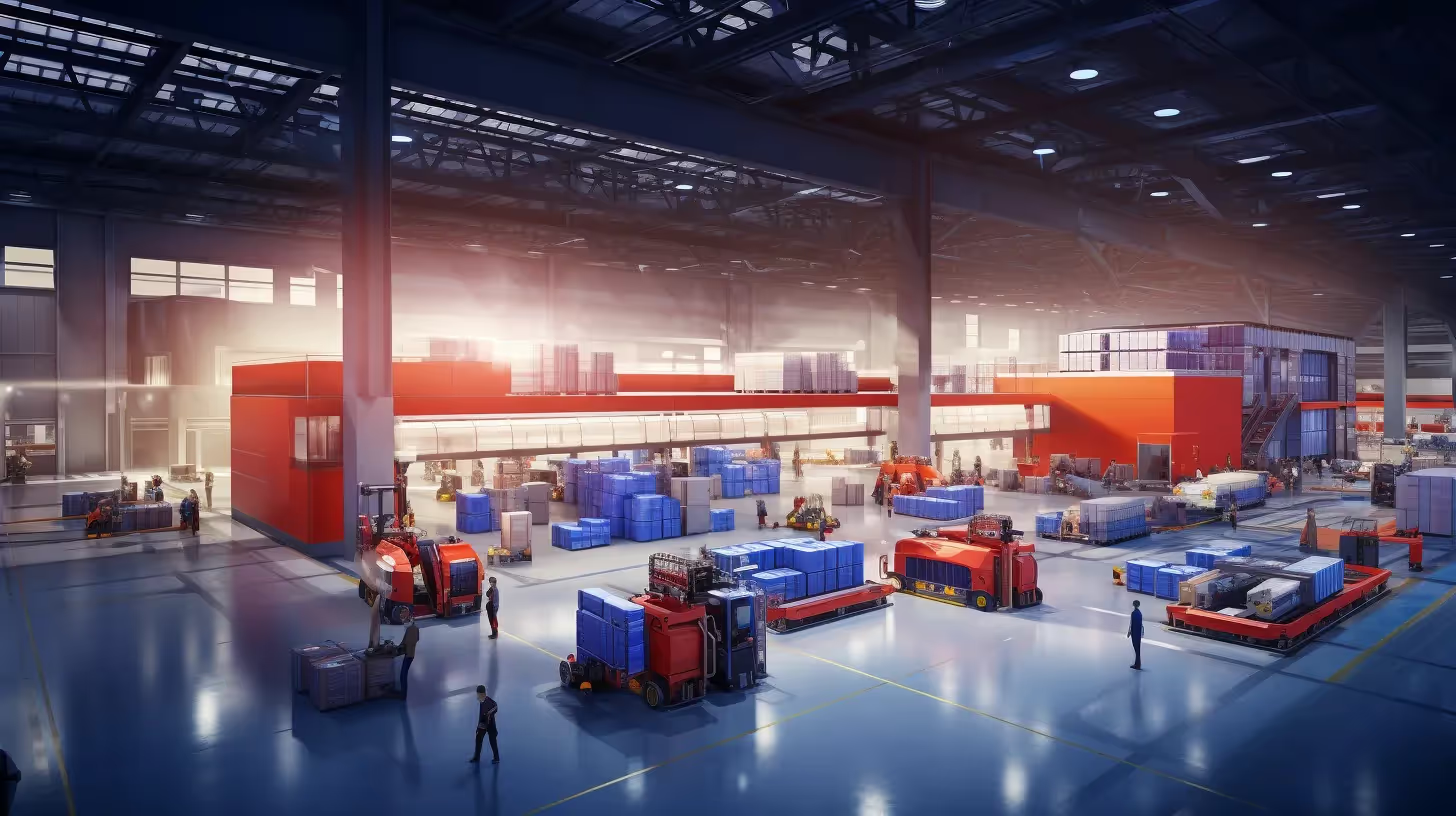
Refurbishment and Repair
Refurbishment and repair are essential processes within reverse logistics that focus on returning returned or damaged products to a usable or sellable state. Here's a closer look at the significance of refurbishment and repair in the context of IT asset management:
Extending Product Lifecycle
Refurbishment and repair processes extend the lifecycle of IT assets. Rather than discarding slightly damaged or outdated products, these processes enable companies to salvage and reuse them.
Cost Savings
Repairing and refurbishing IT assets is often more cost-effective than purchasing new ones. It helps companies save on procurement costs while maintaining operational efficiency.
Sustainable Practices
Refurbishment and repair contribute to sustainability efforts by reducing electronic waste. By reusing and repairing IT equipment, companies reduce their environmental footprint.
Quality Control
During refurbishment, strict quality control measures are implemented to ensure that the repaired or refurbished products meet or exceed industry standards.
Timely Deployment
Efficient repair and refurbishment processes ensure that IT assets are quickly deployed into the organization's infrastructure, minimizing downtime.
Customization
Refurbishment can include customizations based on the organization's specific needs. This allows companies to tailor IT assets to their requirements without the cost of new purchases.
Compliance
Refurbishment processes should adhere to regulatory and industry-specific compliance standards to ensure that repaired equipment meets legal requirements.
Warranty Support
Repaired and refurbished products may come with warranties or guarantees, providing peace of mind to organizations that choose these cost-effective options.
Recycling and Disposal
Recycling and disposal are critical components of reverse logistics and IT asset management, focusing on the environmentally responsible handling of end-of-life products. Here's why recycling and disposal matter:
Environmental Responsibility
Recycling and disposing of IT assets in an eco-friendly manner demonstrate a commitment to environmental responsibility. It reduces the impact of electronic waste on the planet.
Regulatory Compliance
Companies must adhere to regulatory requirements when it comes to electronic waste disposal. Compliance ensures that the disposal process follows legal guidelines.
Data Security
Proper disposal includes data sanitization and secure data destruction. Ensuring that sensitive data is not accessible on disposed assets is essential for protecting sensitive information.
Resource Recovery
Recycling allows for recovering valuable resources from IT assets, such as metals and rare materials. This reduces the need for mining and conserves natural resources.
Landfill Reduction
Responsible disposal practices help reduce the amount of electronic waste in landfills, which can have harmful environmental consequences.
Certified Recycling Facilities
Choosing certified recycling facilities ensures that industry standards and environmental best practices carry out disposal.
Circular Economy
Recycling contributes to a circular economy, where products and materials are reused and recycled, minimizing waste and promoting sustainability.
Public Image
A commitment to responsible recycling and disposal positively impacts a company's public image and sustainability efforts.
For more information on how UCS Logistics handles recycling and disposal responsibly as part of comprehensive IT asset management solutions, please visit our website.
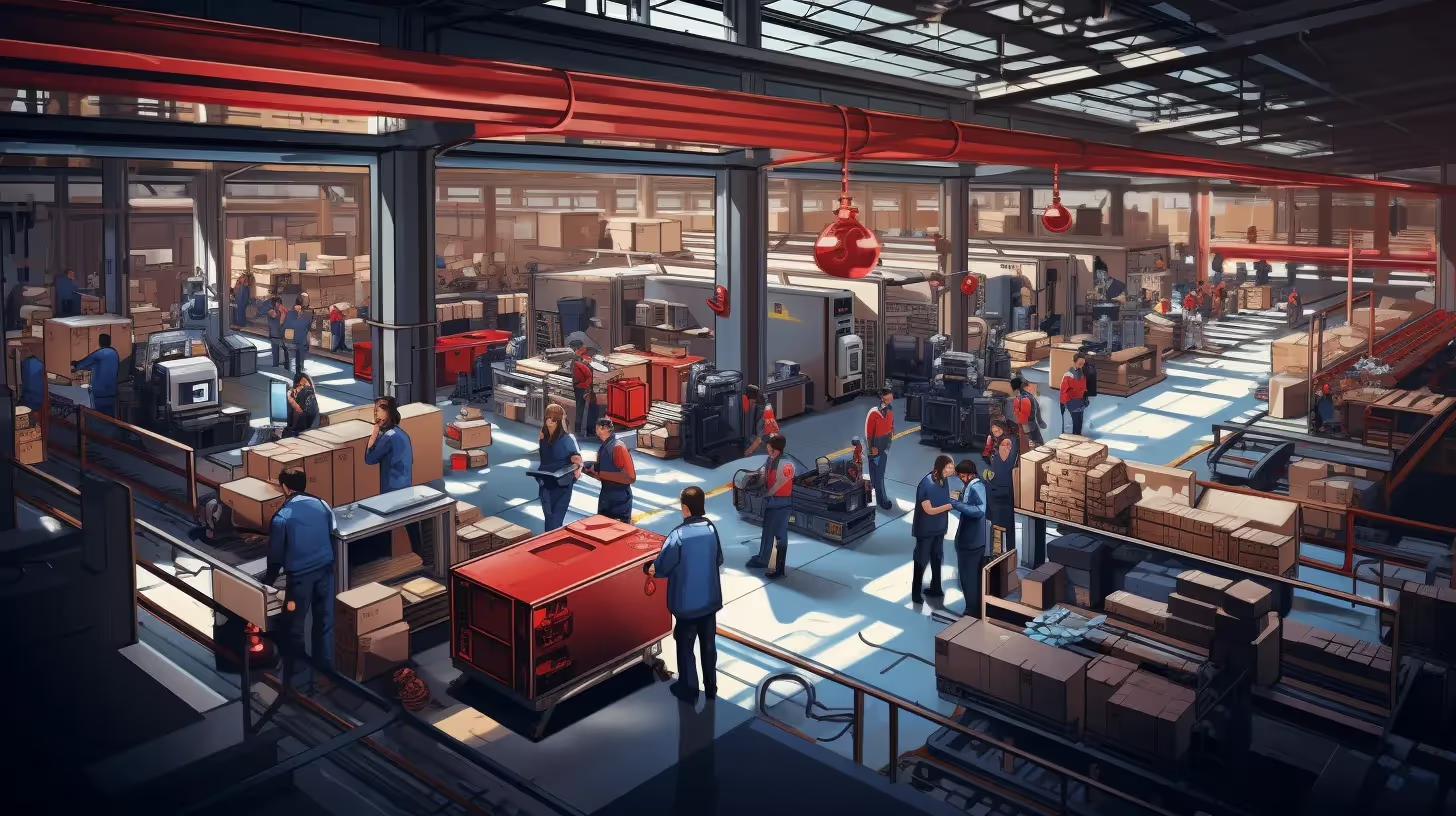
Transportation Efficiency
Transportation efficiency is a crucial aspect of reverse logistics and IT asset management, focusing on optimizing the movement of products and materials within the supply chain. Here's why transportation efficiency is essential:
Cost Reduction
Efficient transportation practices help reduce shipping costs associated with returning, refurbishing, and distributing IT assets. This translates into cost savings for organizations.
Timely Product Delivery
Efficient transportation ensures that returned or refurbished IT assets are delivered to their destinations promptly. This minimizes delays and downtime for organizations.
Minimized Carbon Footprint
Streamlining transportation routes and methods can minimize the carbon footprint associated with logistics operations. This aligns with sustainability goals.
Route Optimization
Route optimization technologies help identify the most efficient routes for transporting IT assets, reducing fuel consumption and transportation time.
Inventory Flow
Efficient transportation is linked to inventory management. Ensuring products are transported to the right locations at the right time helps maintain an optimized inventory flow.
Collaboration with Carriers
Collaboration with transportation carriers and logistics partners is essential for achieving transportation efficiency. Partnerships can lead to cost-effective solutions.
Compliance with Regulations
Efficient transportation practices should comply with regulations and standards, ensuring safe and secure shipments.
Customer Satisfaction
Timely and efficient transportation contributes to customer satisfaction by ensuring that products are available when needed, reducing disruptions.
Customer Communication
Effective customer communication is critical to reverse logistics and IT asset management, focusing on building trust and ensuring a positive customer experience. Here's why customer communication matters:
Transparency
Transparent communication regarding return processes, expected timelines, and policies fosters trust between organizations and customers.
Updates on Returns
Providing customers with regular updates on the status of their returns helps manage expectations and reduces uncertainty.
Return Policies
Clear and concise communication of return policies helps customers understand their rights and responsibilities when returning products.
Feedback Mechanisms
Establishing feedback mechanisms allows customers to provide input on their return experience, enabling organizations to improve.
Resolution of Issues
Effective communication channels enable quick resolution of any issues or concerns that customers may have during the return process.
Building Loyalty
Positive communication experiences contribute to customer loyalty, vital for long-term business success.
Educating Customers
Informing customers about the importance of responsible disposal and recycling of IT assets promotes sustainability and environmental responsibility.
Accessibility
Ensuring customer communication channels are accessible and user-friendly enhances the overall customer experience.
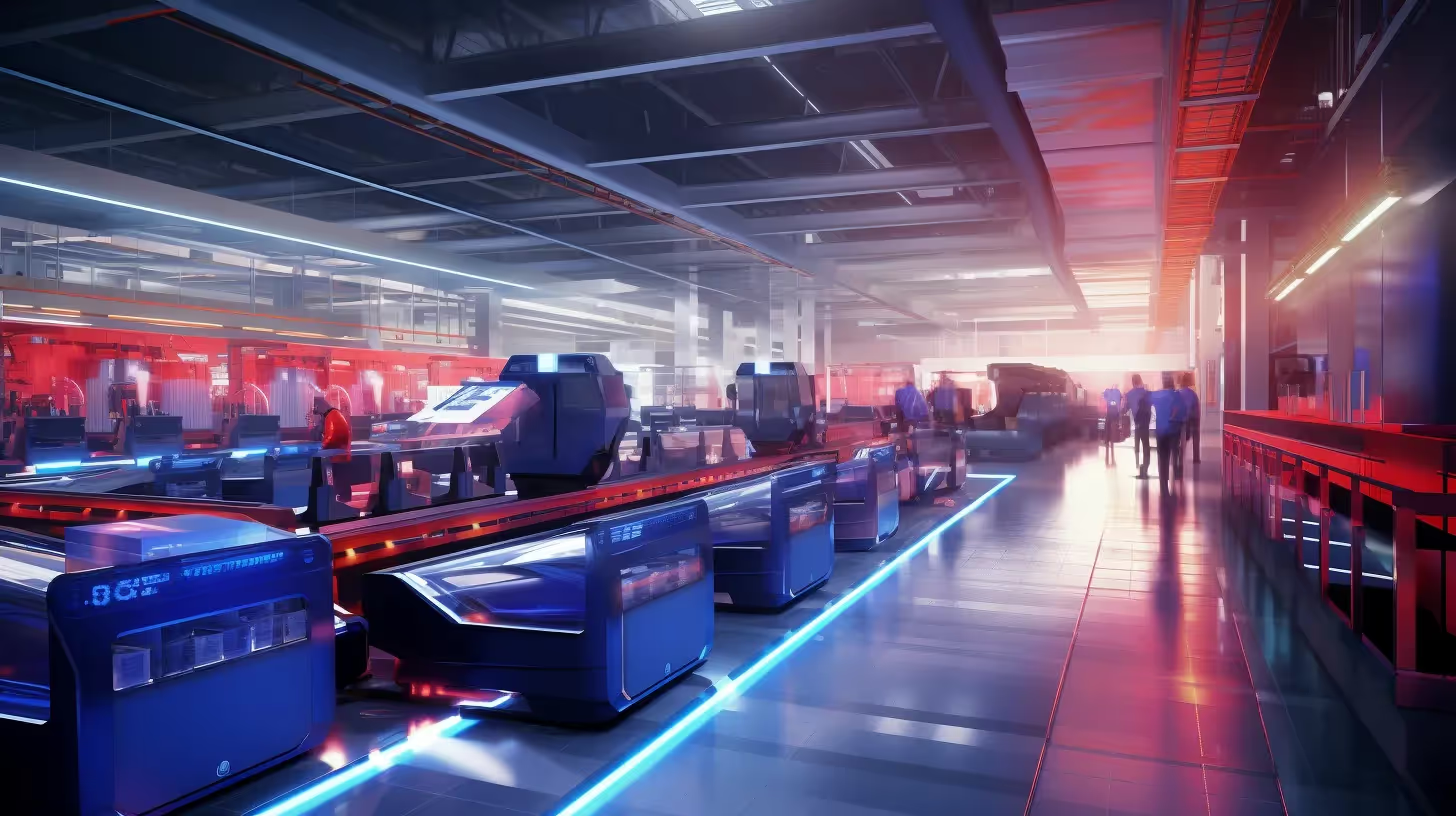
Conclusion
In conclusion, IT asset management is rapidly evolving, and organizations must adapt to stay competitive. The nine best practices in reverse logistics discussed in this article provide a roadmap for success. Whether seeking to optimize returns, improve inventory management, or enhance customer communication, UCS Logistics is here to help.
Our commitment to transparency, sustainability, and customer satisfaction sets us apart. By choosing UCS Logistics, you can access a wealth of expertise and resources to transform your IT asset management processes. Together, we can unlock the full potential of your IT assets, reduce costs, and drive efficiency within your organization.
To embark on a seamless IT asset management journey, visit our website for more information. Contact us today, and let's take your IT asset management to the next level.
Key Takeaways from the Article
Definition and Importance of Reverse Logistics
Reverse logistics is a critical part of supply chain management, involving the return of products to the manufacturer or a designated location for various purposes like refurbishment or recycling.
Effective Returns Management
Key to reverse logistics, it includes processes like return authorization, inspection, evaluation, restocking, refurbishment, repair, and customer communication to minimize costs and maximize customer satisfaction.
Product Evaluation and Sorting
This involves assessing returned products' condition, sorting for resale, refurbishment, recycling, disposal, and efficient inventory management, backed by data analytics for process improvement.
Inventory Management
Crucial for handling returned products efficiently, it covers organized tracking, avoiding overstocking, preventing understocking, prioritizing resale, timely handling, and integrating with other systems for smooth operations.
Data Analytics in Reverse Logistics
Offers insights into return trends, process improvement, inventory optimization, customer behavior analysis, demand forecasting, and integrates with other systems for informed decision-making.
Supplier Collaboration
Essential for optimizing reverse logistics, it involves streamlining returns, managing defective products, addressing excess inventory, ensuring timely replacements, reducing costs, and improving quality and sustainability through continuous improvement.
Refurbishment and Repair
Focuses on returning damaged products to a usable state, extending product lifecycle, saving costs, promoting sustainability, maintaining quality control, ensuring timely deployment, customization, compliance, and warranty support.
Recycling and Disposal
Vital for handling end-of-life products responsibly, ensuring environmental responsibility, regulatory compliance, data security, resource recovery, landfill reduction, using certified facilities, and contributing to a circular economy.
Transportation Efficiency
Aims to optimize product movement within the supply chain, reducing costs, ensuring timely delivery, minimizing carbon footprint, optimizing routes, managing inventory flow, collaborating with carriers, and complying with regulations.
Effective Customer Communication
Critical for building trust and ensuring a positive experience, it involves transparency, regular updates, clear return policies, feedback mechanisms, issue resolution, building loyalty, educating customers, and ensuring accessibility.
Reminder of the Post’s Main Point: The article from UCS Logistics provides a comprehensive guide on best practices in reverse logistics to enhance efficiency, sustainability, and customer satisfaction in IT asset management.
Related Searches
What is Reverse Logistics in Supply Chain Management?
Best Practices in IT Asset Management
Effective Strategies for Customer Satisfaction in Logistics
Role of Data Analytics in Supply Chain Optimization
Sustainable Practices in Electronic Waste Management